How to choose between Hard Chrome Plating vs PVD CrN Coating?
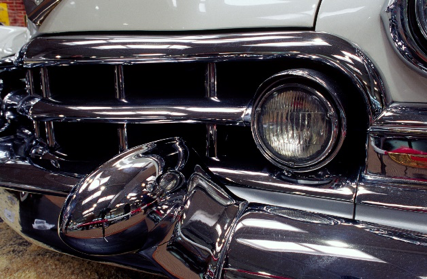
To improve the surface hardness and wear resistance of metallic components, molds, dies, sliding or transmission parts, etc., engineers get to choose between the “hard chrome plating” and the “PVD CrN coating”.
The hard chrome plating relies on an electrochemical reaction to deposit metallic Cr on metal surface. The PVD CrN technology relies on a plasma reaction to deposit ceramic chromium nitride thin films on metal surfaces in vacuum.
Both Cr and CrN provide sufficient hardness and wear resistance to general wear protection and forming/shaping process. Both provide great corrosion resistance and low friction properties to metal surfaces.
However, Cr and CrN are different materials. CrN is twice as hard as Cr. PVD-coated CrN thin film is dense and crack-free, because of its compressive residual stress accumulated during the vacuum plasma deposition process.
The electroplated Cr possesses scattered micro-cracks and defects due to the tensile residual stress within the plating. So, when choosing the right process for your components or tools, here are a few considerations for your reference:
Choose Hard Chrome Plating IF:
- You are handling large size components and tools, or
- You need thick or cover-up coatings with very fine surface finish, or
- You need only a baseline hardness improvement about HRC 60-70
Choose PVD CrN Coating IF:
- You need a super-hard coating, twice as hard as the hard chrome plating, or
- You need to keep tight tolerance and conformal coverage on your tools, or
- You want to retain the sharp edge of your tools, or
- You need extra corrosion/oxidation resistance and mold-releasing property, or
- You need to keep your tools away from Cr+6 contamination, or
- You need to comply with tighter environmental regulations of your processing method
Upgrade to or Integrate with PVD Coating
In terms of a full-service or one-stop surface modification, the modern PVD coating technology can be an integrated part of existing heat treatment or electroplating job shops. The heat treatment is actually a precursor to PVD coatings.
Without a baseline hardness set by heat treatment, PVD won’t be effective as an ultra-thin layer. So, the heat treatment and PVD coating can line up as a continuous process in a single job shop. The market is well-segmented between the PVD coating and the hard chrome plating as well. The unit price is no longer a factor to choose electroplating, because of the justification by its rising cost of waste managements.
The role of a PVD coating service in a plating facility is actually an extension of service toward customers requiring more sophisticated ultra-thin and ultra-hard coatings for the most demanding working condition.
Aurora Scientific Corp. backed with its 30-year field experience in PVD coating service and PVD turn-key system manufacturing would like to provide customized consultation to heat treatment and plating industries seeking an upgrade or an integration toward PVD coating technology.